Sheldon Apgar is known around TA-55 for being the go-to problem solver for equipment in the Plutonium Facility (PF-4) and other area laboratories. As a designer/drafter in the Actinide Materials Processing & Power (AMPP-4) group, he plays a key role in keeping PF-4 up and running.
In 1996 he joined the Laboratory as a glovebox worker, but because he took a few classes on the drafting and design software AutoCAD in high school, it wasn’t long before he was pulled in to help with design projects to improve gloveboxes. He says that when he took the AutoCAD classes, he never thought he’d do anything with it. But 24 years later, he’s the local AutoCAD expert and has built a career on drafting and design.
On a typical day at TA-55, Sheldon and his team spend their time designing new equipment used inside gloveboxes — the large, sealed containers that protect workers from special nuclear materials.
“Typically, the majority of the equipment we work on is inside the glovebox and known as ‘process equipment,’” he says. “The type of equipment we design has to do a certain function that is likely only done at TA-55. This type of work isn’t done anywhere else in the world, so we can’t go to a catalog to order our equipment.”
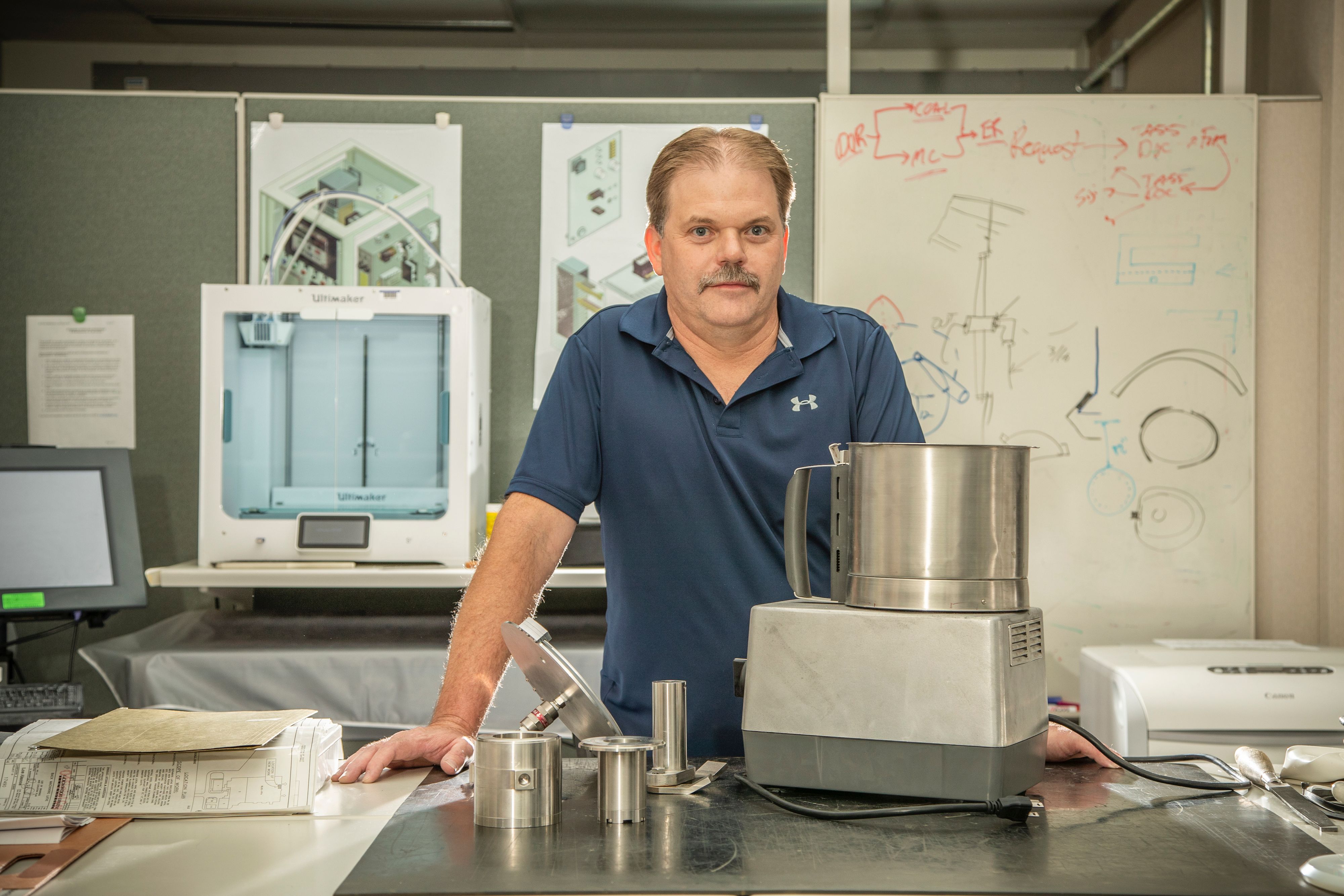
Watching and learning
Occasionally, the AMPP-4 team designs modifications to make existing equipment work for its purposes. In addition to the physical design, Sheldon and his colleagues also have to constantly factor in the atmosphere within the glovebox, including considerations for heat, material characteristics and the possibility for corrosion.
Sheldon says he is grateful for all the colleagues who have helped him understand the science over the years.
“The people I’ve worked with have always been good to help explain these chemical processes to me, since that has never been my background,” he says. “They took the time to show me how things work — not just tell me — and that’s helped me to gain a good understanding.”
“The type of equipment we design has to do a certain function that is likely only done at TA-55. This type of work isn’t done anywhere else in the world, so we can’t go to a catalog to order our equipment.”
Sheldon takes the same approach now of showing versus telling. With everyone from his design teammates to technicians working in the facility to students he mentors, he takes the time to slow down and teach others. “It’s gratifying to see the next generation come in [to work at the Lab],” he says. “I’ve been really impressed with their willingness to learn and ask questions.”
Focused on supporting the worker
While the job title Designer/Drafter might conjure a picture of someone sitting in front of a computer screen all day, Sheldon is known for being on the facility floor, working to understand gloveboxes and the challenges faced by those who work with them. If someone has an issue, he’s often the first person to drop what he’s doing, head to the glovebox and try to figure out a solution.
“Working inside a glovebox complicates a person’s ability to put parts together, so I try to make it simple for them,” he says. “We need this equipment to be functional to support the actual worker.”
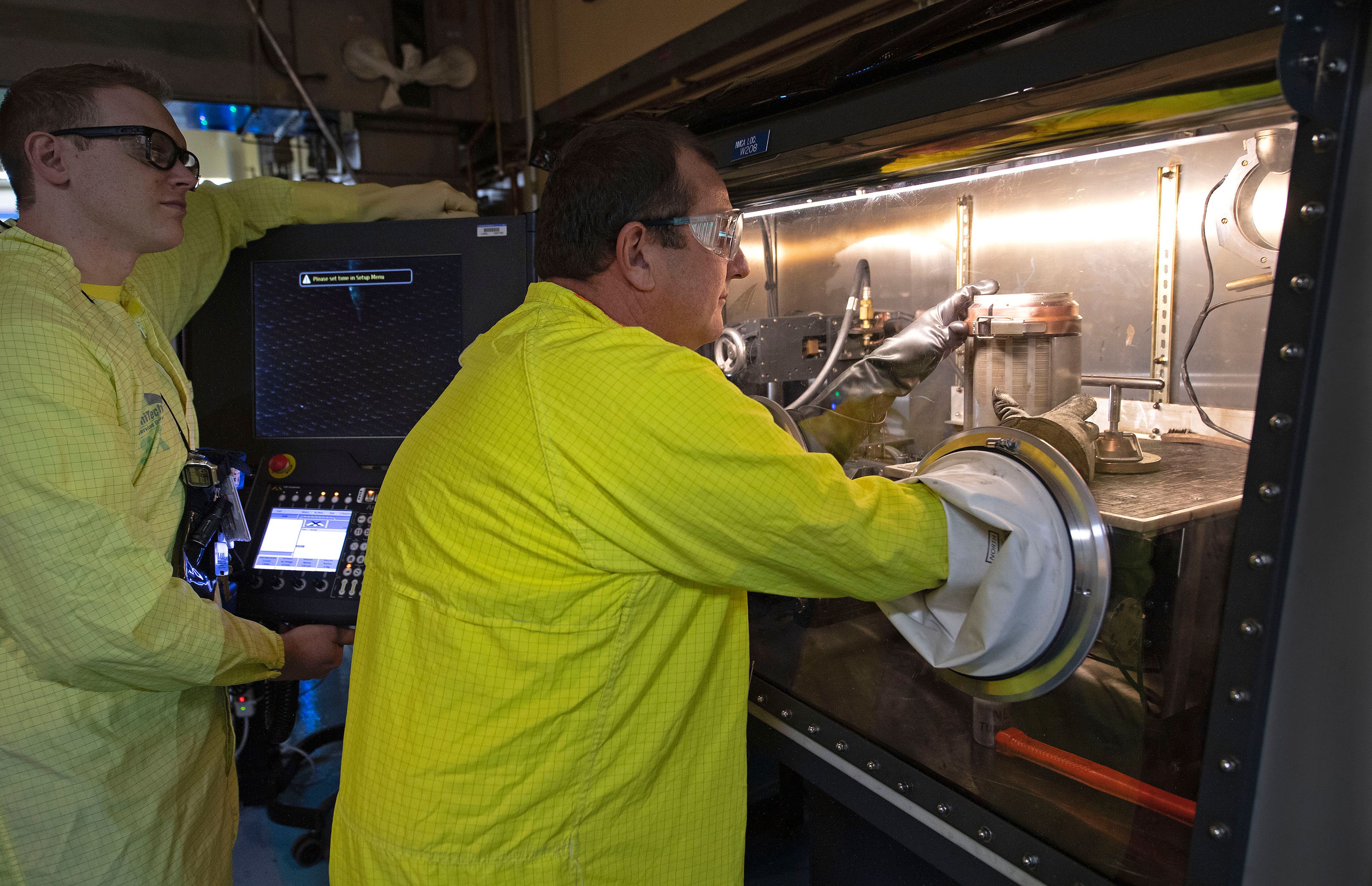
Getting work done inside a glovebox is no easy feat, and Sheldon’s approach to design helps workers because he understands the problems from first-hand experience. He describes glovebox working as being a constant challenge of restricted dexterity, limited reach and limited view. Anything from fastening a bolt to tearing a piece of tape is difficult inside a glovebox.
“Imagine putting your big, heavy winter gloves on, picking up a sewing needle off a table and threading it at arm’s length in front of you,” he explains. “That would be easier than some of the things that glovebox workers have to do in a glovebox.”
When it comes to helping an employee with an equipment issue, he says his first step is to look at the big picture while getting hands-on with the situation. He weighs urgency and necessity alongside his perspective of what else is going on in the facility in order to determine a path forward. Over the years, he’s become so deeply familiar with the equipment in PF-4 that his knowledge allows him to make decisions about whether a glovebox needs a quick fix or a long-term overhaul.
Go-to guy
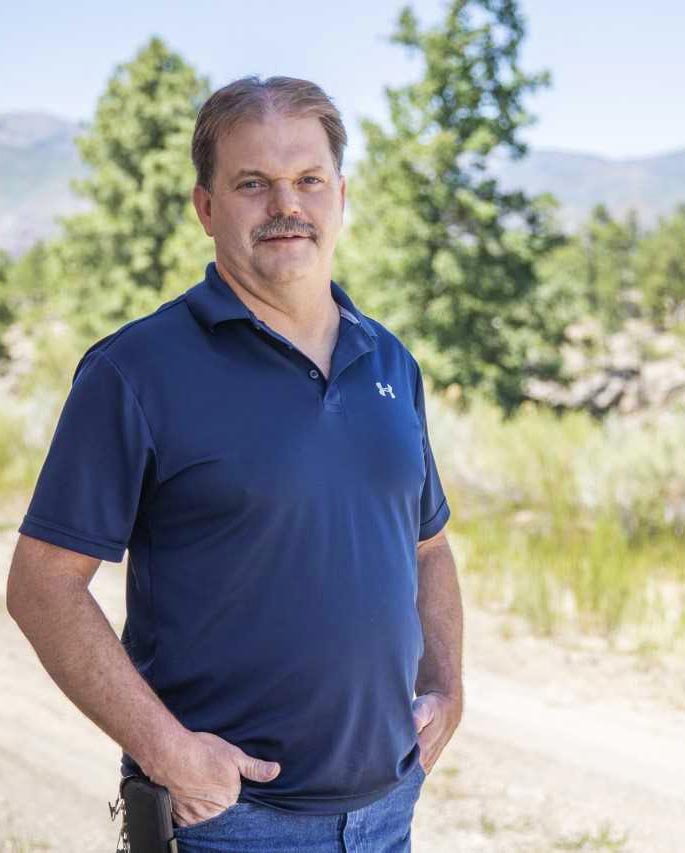
Sheldon and his team have a reputation around the Laboratory for their innovative solutions to unique problems. From partnering with the Facilities and Operations Directorate for the equipment that benefits glovebox processes, to designing for projects outside of his normal scope of work (such as equipment for waste drum characterization), he has a broad perspective on the work at the Lab and the solutions to improve all sorts of processes.
Kent Abney, AMPP-4 group leader, has seen Sheldon’s problem-solving prowess in action for many years. “Our teams rely on Sheldon as the go-to problem solver and solution maker for our organization. He routinely provides creative solutions and exceptional design for multiple programs and organizations around TA-55 and the Lab.”
Gabi Ambrosio and Dave Kimball observe Sheldon’s work up close. Dave recollects a time when a contaminated device had to be replaced, which required a new procedure’s approval before work could begin. “It took more than a year to get the procedure approved to do the work in the Plutonium Facility. But it took Sheldon less than three hours to actually do the work itself, and do it perfectly the first time.”
Gabi has had similar experiences as she and Sheldon worked together on replacing and repairing equipment. When a part in a solvent extraction contactor broke unexpectedly in Gabi’s area, she says that Sheldon was pivotal in solving the problem. “He was able to work with many different organizations to brainstorm possible causes, and multiple paths forward. Sheldon’s mechanical knowledge and glovebox experience make him a great resource for a large array of issues that arise in the facility.”
TA-55 family legacy
Sheldon’s father, Stewart Apgar, started working at the Lab in 1949. While their jobs never overlapped formally, his dad retired from a group at TA-55 where he also did glovebox work, after working at the old plutonium plant on DP Road. Growing up with a parent who worked at TA-55 gave him an early understanding of the atmosphere of working at the Lab.
Today, Sheldon tries to pass that same sense of a broad understanding on to his colleagues, including student mentees and new employees.
“People come to me with questions because they know I can answer them faster than they can dig it up in a document,” Sheldon says. “It’s important to pass that type of knowledge on.”
LA-UR-20-30461